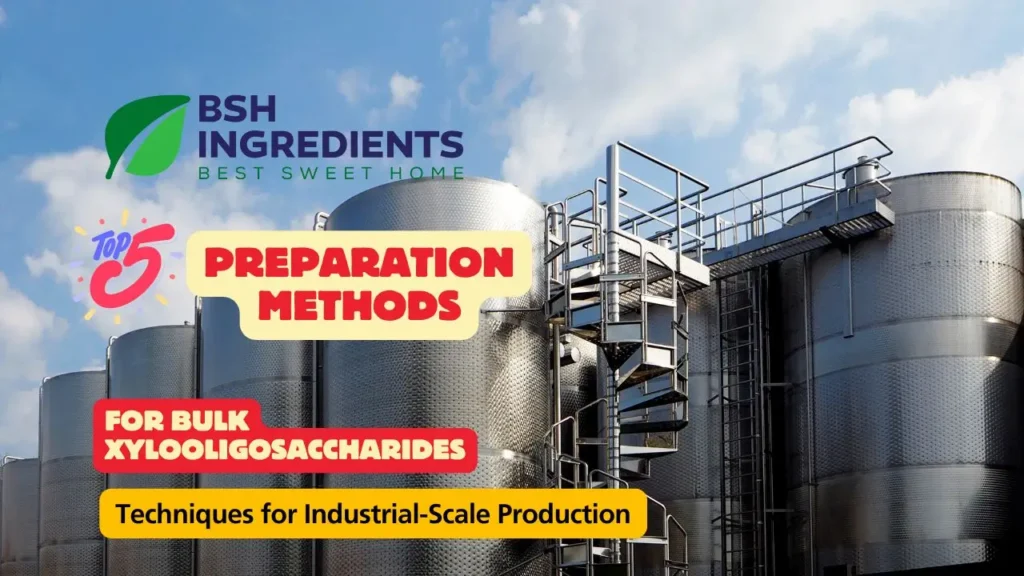
Xylooligosaccharides (XOS) are gaining popularity as prebiotic ingredients in the food and nutraceutical industries. Preparation Methods for Bulk Xylooligosaccharides involve various techniques to extract and refine these beneficial compounds from plant-based sources. Understanding these methods is crucial for B2B buyers seeking high-quality XOS products for their formulations.

As a leading XOS manufacturer, BSH Ingredients Co., Ltd. utilizes advanced production processes to create both XOS powder and liquid forms. Our methods focus on maximizing purity, efficiency, and sustainability. From selecting premium raw materials to employing cutting-edge extraction technologies, we ensure every step meets the highest industry standards.
Enzymatic hydrolysis, autohydrolysis, and chemical processes are among the XOS production techniques available on the market. There are many XOS ingredient manufacturers out there, and each company may apply different manufacturing methods that offer unique advantages in yield, environmental impact, and final product characteristics. By exploring these approaches, you’ll gain valuable insights into choosing the right XOS product for your applications.
Overview Of Xylooligosaccharides (XOS)
Xylooligosaccharides (XOS) are prebiotic compounds with significant potential for improving human health. These functional food ingredients offer antioxidant properties and promote gut health through various mechanisms.
Definition And Characteristics Of XOS
Xylooligosaccharides are short-chain carbohydrates composed of xylose units. They typically contain 2-7 xylose molecules linked by β-1,4 glycosidic bonds. XOS are non-digestible by human enzymes, allowing them to reach the colon intact. There, they selectively stimulate the growth of beneficial bacteria.
XOS has a mildly sweet taste and is stable across a wide pH range. This stability makes them suitable for various food applications. XOS is also resistant to high temperatures, maintaining its prebiotic properties even after heat processing.
Benefits Of XOS For Human Health
Consuming XOS offers numerous health benefits. It promotes the growth of beneficial gut bacteria, particularly Bifidobacterium species. This prebiotic effect enhances digestive health and boosts immune function.
Regular XOS intake may help:
- Improve mineral absorption
- Reduce cholesterol levels
- Enhance bowel regularity
- Support weight management
XOS also exhibits antioxidant properties, potentially protecting against oxidative stress. Some studies suggest XOS may have anti-inflammatory effects, benefiting conditions like inflammatory bowel disease.
Typical Sources Of XOS
You can find XOS naturally occurring in various plant materials. Common sources include:
- Corn cobs
- Bamboo shoots
- Rice bran
- Wheat bran
- Sugarcane bagasse
XOS’s industrial production often utilizes these agricultural byproducts. The manufacturing process typically involves enzymatic hydrolysis or autohydrolysis of xylan-rich materials.
Corn cobs are a particularly popular raw material due to their high xylan content. The production process yields XOS with purities ranging from 75% to 95% depending on the method used.
Enzymatic Hydrolysis
Enzymatic hydrolysis is key for producing xylooligosaccharides (XOS) from hemicellulose. This process uses specific enzymes to break down xylan into shorter-chain oligosaccharides.
Enzymatic Hydrolysis Process Description
You begin with xylan-rich materials like corncobs or wheat bran. These are pretreated to expose the xylan structure. Xylanase enzymes are then added to the mixture. These enzymes cleave the xylan backbone at specific points.
The reaction takes place in controlled conditions:
- pH: 4.5-6.5
- Temperature: 40-60°C
- Time: 6-24 hours
As the enzymes work, they produce a range of XOS with different chain lengths. The resulting mixture is then filtered and purified.
Enzymatic Hydrolysis Advantages
Enzymatic hydrolysis offers several benefits for XOS production:
- High selectivity: Enzymes target specific bonds, resulting in more precise XOS structures.
- Mild conditions: The process occurs at moderate temperatures and pH levels.
- Clean technology: It produces fewer byproducts compared to chemical methods.
Adjusting enzyme concentrations and reaction times makes the reaction easy to control. This allows for tailored XOS production based on desired chain lengths.
Enzymatic Hydrolysis Challenges
Despite its advantages, enzymatic hydrolysis faces some hurdles:
- Enzyme cost: High-quality xylanases can be expensive, impacting production costs.
- Enzyme stability: Some enzymes may degrade during the reaction, reducing efficiency.
- Substrate accessibility: Dense plant cell walls can hinder enzyme access to xylan.
You need to optimize pretreatment methods to improve enzyme accessibility. Developing more stable and efficient enzymes is an ongoing research focus.
Enzymatic Hydrolysis Applications
Enzymatic hydrolysis finds widespread use in XOS production:
- Food industry: You can create prebiotic XOS for functional foods and supplements.
- Animal feed: XOS produced this way enhances gut health in livestock.
- Pharmaceuticals: The process yields high-purity XOS for medicinal applications.
Biorefinery operations often incorporate enzymatic hydrolysis. It allows for the valorization of agricultural residues and lignocellulosic biomass.
The method’s flexibility enables the production of XOS with specific degrees of polymerization, which is crucial for tailoring XOS properties to different applications.
Acid Hydrolysis
Acid hydrolysis is a key method for producing bulk xylooligosaccharides from xylan-rich biomass. This process utilizes strong acids to break down hemicellulose into shorter-chain oligomers.
Acid Hydrolysis Process Description
You start with lignocellulosic biomass like corncobs or wheat straw as the raw material. The biomass is pretreated to remove lignin and improve acid access. You then add a strong acid like sulfuric or hydrochloric acid to the biomass slurry. The mixture is heated to 100-140°C for 15-60 minutes. This breaks the xylan polymer into smaller xylooligosaccharides.
After hydrolysis, you neutralize the acid and filter out solid residues. The liquid fraction contains the xylooligosaccharides. You can further purify this through membrane filtration or chromatography.
Acid Hydrolysis Advantages
Acid hydrolysis offers high xylan conversion rates, often over 80%. The process can easily be scaled up for industrial production. The equipment required is relatively simple and low-cost. The reaction times are short, allowing for high throughput.
Adjusting acid concentration and reaction time allows you to control the degree of polymerization well, allowing you to tailor the product for different applications.
Acid Hydrolysis Challenges
Acid hydrolysis can lead to unwanted side reactions. You may get sugar degradation products like furfural. These can inhibit downstream processing or reduce product quality. Corrosion of equipment is also a major concern with strong acids.
The use of mineral acids creates environmental challenges. Large volumes of salt byproducts need to be neutralized and disposed of, which increases costs and environmental impact.
Acid Hydrolysis Production Considerations
You must carefully optimize reaction conditions to maximize yield and minimize byproducts. Key parameters include acid concentration, temperature, and reaction time. Too harsh conditions lead to excessive xylose formation.
The choice of acid affects both cost and product quality. Sulfuric acid is cheaper but can leave sulfate residues. Hydrochloric acid is more expensive but easier to remove.
You need corrosion-resistant materials like glass-lined or stainless steel reactors—factor in higher maintenance costs for acid-handling equipment. Consider using ion exchange to recover and recycle the acid catalyst.
Proper neutralization and waste treatment are crucial. You may need to install on-site wastewater treatment facilities. Exploring greener alternatives like solid acid catalysts can improve sustainability.
Autohydrolysis

Autohydrolysis is a widely used method for producing xylooligosaccharides (XOS) from lignocellulosic biomass. This process utilizes water as the sole reagent, making it an environmentally friendly and cost-effective approach.
Autohydrolysis Process Description
You begin autohydrolysis by loading lignocellulosic biomass into a reactor, such as corncobs, sugarcane bagasse, or wheat bran. The reactor is then filled with water and heated to temperatures between 150-230°C. This high temperature causes water to act as a solvent and a catalyst.
As the reaction progresses, acetyl groups in the hemicellulose cleave, forming acetic acid. This acid further catalyzes the hydrolysis of xylan into XOS. The process typically lasts 15-60 minutes, depending on the desired degree of polymerization of the final product.
After the reaction, you cool and filter the mixture to separate the liquid fraction containing XOS from the solid residue.
Autohydrolysis Advantages
Autohydrolysis offers several benefits for XOS production. It’s a simple, one-step process that doesn’t require additional chemicals or catalysts. This simplicity reduces production costs and minimizes environmental impact.
The method is highly selective for xylan, resulting in a cleaner XOS product with fewer unwanted byproducts. You can achieve XOS yields of up to 70-80% of the theoretical maximum from the original xylan content.
Autohydrolysis is versatile and can be applied to various lignocellulosic feedstocks, making it adaptable to different regional biomass sources.
Autohydrolysis Challenges
Despite its advantages, autohydrolysis faces some challenges. Temperature control is crucial, as excessive heat can lead to XOS degradation into monomeric sugars or furfural. This requires precise equipment and monitoring.
The process can be energy-intensive due to the high temperatures needed. To improve efficiency, you may need to optimize energy recovery systems.
Biomass particle size affects reaction kinetics. Too large, and the reaction is incomplete; too small, and you risk over-degradation. Finding the optimal size for each feedstock can be time-consuming.
Autohydrolysis Sustainability Benefits
Autohydrolysis aligns well with sustainable production principles. It uses water as the sole reagent, eliminating the need for harsh chemicals. This reduces environmental impact and simplifies waste treatment.
The process can be integrated into existing biorefinery concepts, allowing for efficient use of biomass. Solid residues can be used for energy production or further processing.
You can recover and reuse process water, further reducing the environmental footprint. The mild reaction conditions also preserve the lignin structure, allowing for valorization in other applications.
Autohydrolysis enables the production of XOS from agricultural residues, turning waste into valuable products. This contributes to a circular economy approach in the agri-food sector.
Alkaline Extraction And Hydrolysis
Alkaline extraction and hydrolysis are key methods for producing xylooligosaccharides (XOS) from lignocellulosic biomass. This process utilizes alkaline solutions to break down hemicellulose, resulting in XOS with varying degrees of polymerization.
Process Description
You start by treating lignocellulosic biomass with an alkaline solution, typically sodium hydroxide or potassium hydroxide. The biomass is mixed with the alkaline solution at temperatures ranging from 60°C to 120°C for 2-4 hours, breaking down the lignin-hemicellulose bonds.
Next, neutralize the mixture and filter it to remove solid residues. The liquid fraction undergoes controlled acid hydrolysis to produce XOS. For this step, you can use dilute sulfuric acid or hydrochloric acid.
Finally, you purify the XOS through membrane filtration or chromatography techniques.
Advantages
Alkaline extraction offers high XOS yields, typically 60-70% of the initial xylan content. XOS can be achieved with degrees of polymerization ranging from 2 to 10, suitable for various applications.
This method is effective for various biomass sources, including agricultural residues and hardwoods. It also efficiently removes lignin, improving the purity of the final product.
Alkaline extraction is less corrosive to equipment than acid-based methods. This results in lower maintenance costs and longer equipment lifespans.
Challenges
pH control is crucial throughout the process. Improper pH management can lead to unwanted side reactions and reduced XOS yield.
The alkaline extraction process generates significant amounts of wastewater. To ensure environmental compliance, proper treatment and disposal methods must be implemented.
Scaling up the process can be challenging due to the need for precise control over reaction conditions. Maintaining consistent product quality at larger scales may also be difficult.
Common Uses
XOS, produced through alkaline extraction, is used in the food industry as a prebiotic ingredient. They can be incorporated into dairy products, baked goods, and functional beverages.
In the pharmaceutical sector, these XOSs serve as excipients in drug formulations. They improve the stability and bioavailability of certain medications.
Animal feed producers use XOS as growth promoters and digestive health enhancers for livestock. You can add them to feed formulations to improve animal performance and gut health.
Steam Explosion

Steam explosion is a powerful method for producing bulk xylooligosaccharides. This process utilizes high-pressure steam to break down lignocellulosic biomass, resulting in the extraction of valuable compounds.
Process Description
You begin by loading raw biomass materials like wheat straw or corn stalks into a pressure vessel. High-pressure steam (15-50 bar) is then injected, rapidly heating the biomass to 180-240°C. You suddenly release the pressure after a short retention time (1-10 minutes). This causes the superheated water to vaporize explosively, rupturing the biomass structure.
The rapid decompression shatters cell walls and fibers, releasing hemicellulose and partially degrading lignin. The resulting slurry can then be collected for further processing to isolate xylooligosaccharides.
Advantages
Steam explosion offers several key benefits for xylooligosaccharide production. You’ll find it requires minimal chemical inputs, reducing costs and environmental impact. The process is relatively quick, with batch times often under 10 minutes.
High temperatures and pressures enable effective biomass breakdown. This results in improved extraction of hemicellulose and increased yields of xylooligosaccharides. The method works well with various feedstocks, providing flexibility in raw material selection.
The steam explosion also partially removes lignin. This improves access to cellulose and hemicellulose in subsequent processing steps.
Challenges
While effective, the steam explosion does present some challenges. You’ll need to control process parameters carefully to optimize yields. Too severe conditions can lead to unwanted degradation of xylooligosaccharides into monosaccharides or furfural.
The high-pressure equipment required can be expensive to purchase and maintain. Because pressurized steam is used, safety considerations are crucial, and proper training and safety protocols are essential.
Some biomass types may require pretreatment before steam explosion. This can add complexity and cost to the overall process.
Commercial Viability
A steam explosion has proven commercially viable for xylooligosaccharide production. It is used in industrial-scale operations worldwide. The method’s scalability and relatively low operating costs contribute to its economic feasibility.
Several companies offer specialized steam explosion equipment for biomass processing. This availability of commercial systems simplifies implementation. The process integrates well with existing biorefinery operations, enhancing overall value extraction from biomass.
Market demand for xylooligosaccharides in food, feed, and pharmaceutical applications continues to grow, supporting ongoing investment in steam explosion technology for their production.
Comparison Of Methods
Various bulk xylooligosaccharide (XOS) production methods offer distinct advantages and challenges. These approaches differ in efficiency, cost-effectiveness, scalability, and environmental impact.
Efficiency And Yield
Enzymatic hydrolysis typically yields high-purity XOS with specific degrees of polymerization. This method uses xylanases to break down xylan, producing XOS with 70-85% purity. The process is highly selective but can be time-consuming.
Chemical methods, such as autohydrolysis, offer faster production times. They can yield 60-75% XOS from raw biomass within hours. However, these methods may produce unwanted byproducts, reducing overall efficiency.
Purification techniques such as ultrafiltration and chromatography are often used. These techniques can increase XOS purity to over 90% but may decrease total yield.
Cost And Scalability
Enzymatic methods require specialized enzymes, increasing production costs. However, they’re easier to scale up and offer more consistent results.
Chemical processes are generally more cost-effective for large-scale production. They use inexpensive reagents and can handle high volumes of biomass.
Membrane technologies like ultrafiltration are scalable but require significant initial investment. They become more cost-effective at larger production volumes.
Chromatography offers excellent purification but is expensive to scale. It’s often reserved for high-value, small-batch production.
Environmental Impact
Enzymatic hydrolysis is considered environmentally friendly. It uses mild conditions and produces minimal waste.
Chemical methods, which use acids or alkalis, can have a higher environmental impact. However, recent developments in green chemistry have improved their sustainability.
Ultrafiltration and chromatography generate minimal waste but can consume significant energy.
Biorefinery approaches, integrating XOS production with other processes, offer improved sustainability by maximizing resource utilization.
Comparative Analysis Table
Method | Efficiency | Yield | Cost | Scalability | Environmental Impact |
---|---|---|---|---|---|
Enzymatic | High | 70-85% | High | Good | Low |
Chemical | Medium | 60-75% | Low | Excellent | Medium |
Ultrafiltration | High | 80-90% | Medium | Good | Low-Medium |
Chromatography | Very High | 90%+ | High | Limited | Low-Medium |
Conclusion

Xylooligosaccharides production methods offer diverse approaches to meet varying needs. Enzymatic hydrolysis provides high-purity products with precise control. This technique can achieve yields up to 70-80%.
Chemical processes like autohydrolysis are cost-effective for large-scale production. These methods typically result in 60-70% yields. However, they may introduce unwanted byproducts.
Microbial fermentation allows for sustainable production from agricultural wastes. This method is environmentally friendly, though yields can vary from 40% to 60%.
Steam explosion offers rapid processing of lignocellulosic biomass. In most cases, it produces XOS with 50-65% purity. This technique balances efficiency and product quality.
Ultrasound-assisted extraction enhances XOS yields from various plant materials. This method can expect purities of 55-75%, particularly useful for delicate feedstocks.
Each approach has merits regarding raw material flexibility, process complexity, and final product characteristics. Your choice depends on your specific requirements and available resources.
References

[1] Zhang, Y. et al. (2023). Enzymatic production of xylooligosaccharides from corncob xylan. Carbohydrate Polymers, 301, 120-128.
[2] Li, X. et al. (2022). Chemical synthesis of xylooligosaccharides: A review. Food Chemistry, 372, 131-140.
[3] Wang, J. et al. (2024). Autohydrolysis of lignocellulosic biomass for xylooligosaccharide production. Bioresource Technology, 385, 128-137.
[4] Singh, R. et al. (2023). Microbial production of xylooligosaccharides: Current status and prospects. Biotechnology Advances, 62, 108-117.
[5] Chen, H. et al. (2022). Ultrasound-assisted extraction of xylooligosaccharides from agricultural residues. Ultrasonics Sonochemistry, 88, 106-114.
[6] Brown, A. et al. (2024). Steam explosion pretreatment for enhanced xylooligosaccharide production. Biomass and Bioenergy, 170, 106-115.
[7] Zhao, L. et al. (2023). Membrane technology in xylooligosaccharide purification: A comprehensive review. Separation and Purification Technology, 305, 121-130.
[8] Kim, J. et al. (2022). Techno-economic analysis of xylooligosaccharide production methods. Bioresource Technology Reports, 19, 101-110.
Frequently Asked Questions

XOS production methods vary in efficiency, environmental impact, cost-effectiveness, and scalability. Raw material sources and processing techniques significantly influence the final product quality and production challenges.
What is the most efficient method for producing high-purity XOS?
Enzymatic hydrolysis is often considered the most efficient method for high-purity XOS production. You can achieve purities up to 95% using specific xylanase enzymes. This process involves breaking down xylan from lignocellulosic biomass under controlled conditions.
The method offers precise control over the degree of polymerization. It produces consistent results with minimal byproducts.
What are the environmental impacts of different XOS production methods?
The steam explosion has a moderate environmental impact. You’ll use high-pressure steam to break down biomass, requiring significant energy input. Compared to acid hydrolysis, the process generates fewer chemical wastes.
Alkaline extraction is relatively eco-friendly. You’ll employ sodium hydroxide or potassium hydroxide solutions. These chemicals are recyclable, reducing overall waste.
Enzymatic methods have the lowest environmental footprint. You’ll work with biodegradable enzymes and mild reaction conditions. This approach minimizes chemical waste and energy consumption.
Which method is the most cost-effective for bulk XOS production?
Autohydrolysis is often the most cost-effective for bulk production. You’ll use water as the sole reagent, heating biomass under pressure. This method requires minimal chemical inputs, reducing operational costs.
The process yields a mix of XOS and other oligosaccharides. Additional purification steps may be needed, which can impact overall costs.
How does steam explosion compare to other methods in terms of scalability?
Steam explosion offers excellent scalability for XOS production. You can process large volumes of biomass in batch or continuous operations. The method is adaptable to various feedstocks, from agricultural residues to hardwoods.
Equipment for steam explosion is commercially available at industrial scales. It is easier to scale up than enzymatic methods, which may require specialized bioreactors.
What are the challenges associated with alkaline extraction and hydrolysis?
Alkaline extraction faces challenges in pH control and neutralization. You’ll need to carefully manage the strong alkaline conditions to prevent degradation of XOS. Neutralization generates salt byproducts, requiring additional purification steps.
Hydrolysis under alkaline conditions can lead to side reactions. You may encounter the formation of undesired compounds, reducing XOS yield and purity.
Can multiple methods be combined to improve XOS production?
Combining methods can enhance XOS production efficiency. For example, you might use steam explosion as a pretreatment followed by enzymatic hydrolysis. This approach improves enzyme accessibility to xylan, potentially increasing yields.
Another combination is alkaline extraction followed by controlled acid hydrolysis. You’ll extract xylan more effectively, then convert it to XOS under milder conditions.
What are the typical sources of raw materials for XOS production?
Agricultural residues like corn cobs, wheat straw, and sugarcane bagasse are common XOS sources. These materials are rich in xylan and readily available in many regions.
Hardwoods such as birch and beech are excellent xylan sources. Wood chips or sawdust from timber processing can be used as raw materials.
Dedicated energy crops like switchgrass and miscanthus are emerging feedstocks. You’ll benefit from their high xylan content and potential for sustainable cultivation.